Formulating for the Future
By Neil Forbes
With applications in the automotive, construction, wood, and transportation sectors,1 the global paints and coatings industry represents a hugely valuable segment of the performance chemicals market. In 2023, the global paints and coatings market was valued at $206.56 billion.2 In the UK alone, the British Coatings Federation (BCF) valued it to be worth £3.2 billion.3
Despite its ubiquity, the industry is also one of the most heavily regulated in the world;4 hence, innovation and continuous development are perpetually important for manufacturers to keep pace with regulatory and legislative demands. In recent years, these demands have seen an increased focus on environmental impact and safety, as the industry takes a bigger role in supporting a more sustainable future for us all. 5
Paints, Driers, and Regulations
Due to the sector’s sensitivity to new regulations, legislation has historically helped drive innovation within paints and coatings. A good example of this is the reduction of volatile organic compounds (VOCs) in paints and coatings formulations.6, 7 Stringent restrictions on them, spurred on by environmental and health concerns, have (and continue to) dominate the direction of innovation in paints and coatings.8
More recently, new regulatory attention has been directed towards paint driers – a key additive within paints and coatings that help them to dry, following application. 9 Generally based on metals such as cobalt, copper, iron and strontium, and stabilised by carboxylate ions, paint driers speed up cross-linking between unsaturated regions of alkyd resins used as binders in certain paints. This creates a polymer network that then binds the pigment to the painted surface. Overall, paint driers can cut the drying time of paint from several months to just a few hours.
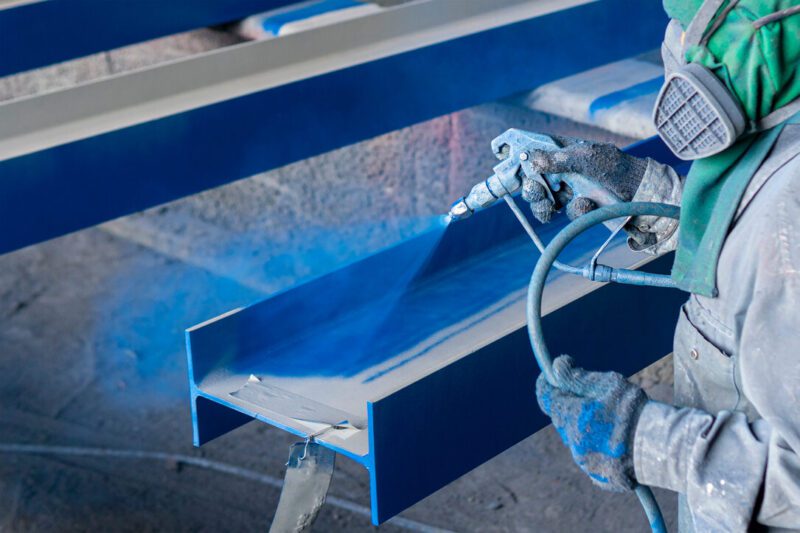
Regulation around paint driers has taken several forms. Common types of paint driers, such as strontium, have recently been the subject of new EU restrictions – with other countries like the UK expected to follow suit in the next few years.10 While these regulations have been driven by safety, issues beyond toxicity have also come to have an impact on the use of specific raw materials within paints and coatings.
Cobalt driers, for example, are one of the most widely used metal paint driers and have been facing increased scrutiny due to a spike in demand and humanitarian concerns surrounding the extraction of the metal used in them.11 In an industry so sensitive to regulation, maintaining sustainable, stable supply chains is critical. That is why businesses are looking towards innovative, novel solutions to build a better value chain. In theory, cobalt should be infinitely recyclable – but only by reusing end-use materials and closing industrial inefficiencies can we hope to find a better, more ethical source of cobalt.
The Galvanised Demand for Cobalt
Cobalt is primarily used in batteries. Over three quarters of the world’s supply is sourced from the Democratic Republic of Congo.12
Due to an increased adoption of electric vehicles and electronic devices, there is currently a higher requirement for cobalt than ever before. In 2023, demand for cobalt reached 200 kt for the first time ever, with electric vehicles representing 45% of this and batteries at nearly 30%. Predictably, the cobalt industry responded to this demand with higher-than-ever output. Market surplus also increased to its highest-ever volume of 14.2 kt in 2023 – over double what it was the previous year.
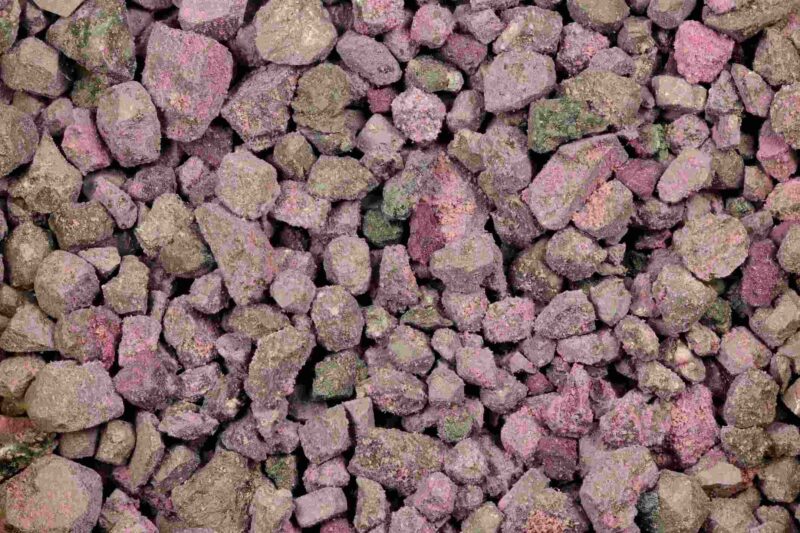
Due to its position as an essential component in electric vehicles, cobalt has also become increasingly intertwined with geopolitics as major economies tussle to secure access to the precious mineral and fulfil their climate neutrality strategies. Already, both the US and EU have classified it as a critical raw material, yet it also topped the Critical Materials Risk Index in 2022, a metric that attempts to quantify supply risk and economic importance.13,14 This highlights cobalt’s precarious position in the market, leaving it potentially exposed to changes in the geopolitical landscape, which could reshape the market in an instant.
Humanitarian considerations within the extraction of cobalt also surround its usage. Its rising demand has placed new attention on issues of governance of the mines and conditions for workers, including in some cases, the use of child labour. This has driven calls to forge a more ethical cobalt supply chain.
The variation in factors impacting the cobalt industry and the inadequate working conditions means that the continued usage of ‘virgin’ cobalt within paints and driers is not assured. As an industry prone to the winds of regulation, manufacturers must be on the lookout for alternative sources of cobalt and replacements to secure their supply – now and into the future.
Using Green Chemistry to forge better Supply Chains with Umicore
In the last 10 years, green chemistry has flourished. The principles underpinning it, first published in 1998, now occupy a significant role in the chemical industry.15 By conserving resources and considering the environmental impact of chemical value chains, green chemistry not only creates a healthier environment but also helps future-proof businesses. Green chemistry has already had a significant impact on the regulation of paints and driers – and will likely continue to do so.
Umicore, a Brussels-based materials business, takes these principles of green chemistry seriously. Named one of TIME’s top 500 most sustainable companies of 2024,16 Umicore seeks to proactively offer customers the choice of more ethical, considerate, supply chains. Since June, Cornelius has been appointed by Umicore to distribute its metal carboxylate drier portfolio in the UK and Ireland. As a company dedicated to responsible consumption and extraction and one that uses innovative solutions to solve industry challenges, Umicore’s range is a natural fit to Cornelius’ portfolio.
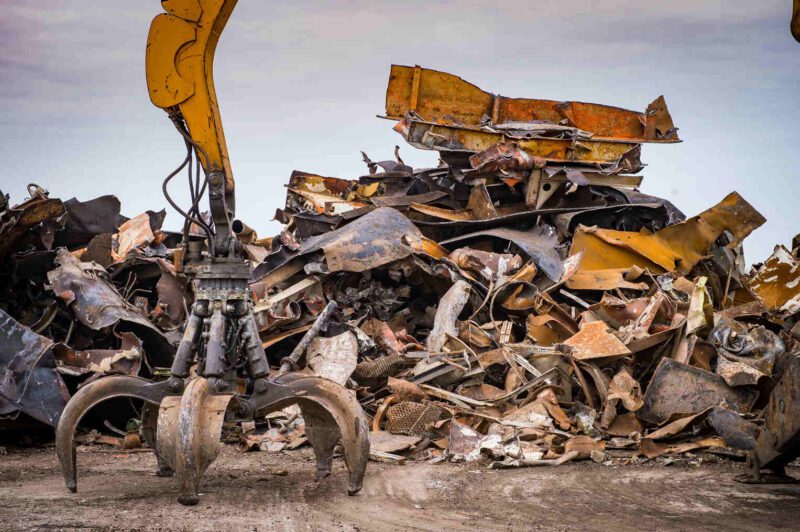
Umicore’s metal reusing capabilities mean that it can recover cobalt from production and processes within manufacturing – such as from hard metal or cemented carbide tools – as well as from end-of-life products such as rechargeable batteries and catalysts. By building these sources into their supply chains, their paints and coatings additives are less dependent on the use of virgin cobalt. Umicore can also apply its patented polymer matrix technology to respond to customers concerned about the health effects of cobalt in formulations as well.
Proud of its supply chain transparency and the affiliations it makes as a company, Umicore is committed to responsible sourcing materials and pays careful attention to the conditions under which they are extracted.
Looking Ahead
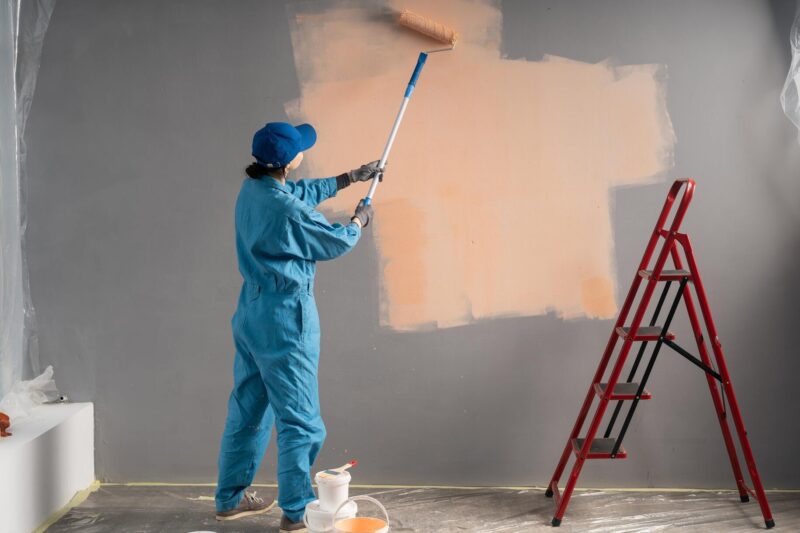
With so many industries resting on paint and coatings, there is no doubt that it is a critical industry. However, it also exists within a robust regulatory landscape prone to legislative changes. It’s for this reason manufacturers must always keep an eye on what could be just around the corner, regulatorily speaking.
While cobalt has become heavily relied on as a drier in paints and coatings, questions about its supply chain are driving the need for alternative routes and solutions. By partnering with innovative companies like Umicore, committed to the principles of green chemistry and who are proactively offering solutions to future issues in the industry, we can help businesses protect their supply chain for the future.
Continued innovation and development within the sector will likely see further shifts away from chemicals deemed unsafe or unethical. This will drive the paints and coatings industry towards providing customers with ever more sustainable, conscientious products.
References
- McGonigle, F. and Ciullo, P. A. (1996) Paints & Coatings. Industrial Minerals and Their Uses. 99-159. Doi: https://doi.org/10.1016/B978-081551408-4.50005-3
- Fortune Business Insights (2024) Paints and Coatings Market Size, Share & Industry Analysis, By Resin (Epoxy, Acrylic, Polyester, Alkyd, Polyurethane, and Others), By Product Type (Waterborne, Solvent Borne, Powder Coatings, UV Coatings and Others) By Application (Architectural, Automotive OEM, Marine, Coil, General Industries, Protective Coatings, Automotive Refinish, Industrial Wood, Packaging, and Others), and Regional Forecast, 2024-2032. Available at: https://www.fortunebusinessinsights.com/industry-reports/paints-and-coatings-market-101947 [Accessed July 2024]
- British Coatings Foundation (2024) Industry Statistics. Available at: https://coatings.org.uk/page/IndustryStatistics [Accessed July 2024]
- S&B Global (2023) Paint and Coatings Industry Overview. Available at: https://www.spglobal.com/commodityinsights/en/ci/products/paint-and-coatings-industry-chemical-economics-handbook.html. [Accessed July 2024]
- Jotischky, H. (2001) ‘Coatings, regulations and the environment reviewed’, Surface Coatings International Part B: Coatings Transactions, 84, pp. 11–20. doi: https://doi.org/10.1007/BF02699691
- The Volatile Organic Compounds in Paints, Varnishes and Vehicle Refinishing Products Regulations 2012 (S I2012/1715). Available at: https://www.legislation.gov.uk/uksi/2012/1715/contents [Accessed July 2024]
- Environmental Protection Agency (2024) Consumer Products: National Volatile Organic Compound Emission Standards. Available at: https://www.epa.gov/stationary-sources-air-pollution/consumer-products-national-volatile-organic-compound-emission [Accessed July 2024]
- Cunningham, M. F. et al. (2019) ‘Future green chemistry and sustainability needs in polymeric coatings’, Green Chemistry, 21(18), pp. 4919-4926. Doi: https://doi.org/10.1039/C9GC02462J
- SpecialChem (2024) Select Driers for High Solids and Waterborne Coatings. Available at: https://coatings.specialchem.com/selection-guide/select-driers-for-high-solids-and-waterborne-coatings [Accessed July 2024]
- European Chemicals Agency (2024) Strontium Substance Infocard. Available at: https://echa.europa.eu/substance-information/-/substanceinfo/100.028.303 [Accessed 2024]
- McQuilken, J., Shirgholami, Z. and McFarlane, D., (2022) ‘Understanding and addressing ‘modern slavery’ in DRC-UK cobalt supply chains’, In Yakovleva, N., Nickless, E. (eds.) Routledge Handbook of the Extractive Industries and Sustainable Development. London: Routledge, pp. 514-541
- Cobalt Institute (2023) Cobalt Market Report 2023. Available at: https://www.cobaltinstitute.org/resource/cobalt-market-report-2023/ [Accessed July 2024]
- Cobalt Institute (2024) Essential Cobalt. Available at: https://www.cobaltinstitute.org/essential-cobalt-2/ [Accessed July 2024]
- Mining.com (2022) Cobalt tops Critical Materials Risk Index. Available at: https://www.mining.com/cobalt-tops-critical-materials-risk-index/ [Accessed July 2024]
- American Chemical Society (2024) 12 Principles of Green Chemistry. Available at: https://www.acs.org/greenchemistry/principles/12-principles-of-green-chemistry.html [Accessed July 2024]
- TIME (2024), World’s Most Sustainable Companies of 2024. Available at: https://time.com/collection/worlds-most-sustainable-companies-2024/ [Accessed July 2024]